USW Members Play Crucial Roles in COVID-19 Vaccine Distribution
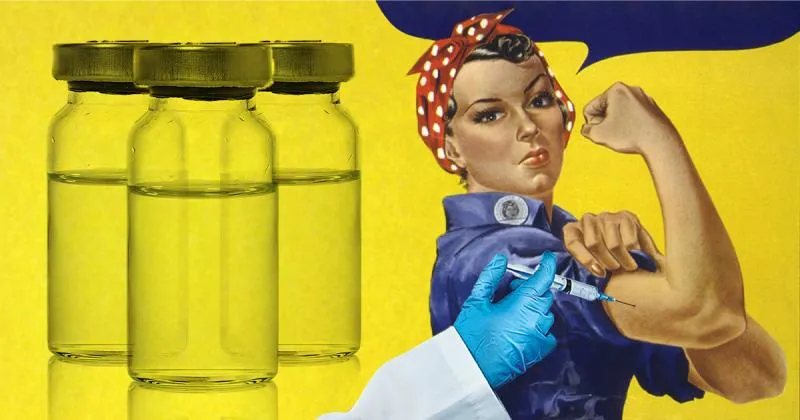
As COVID-19 infection rates soared to ever-higher levels early this year, hundreds of Steelworkers put their lives on the line – and some logged exhausting amounts of overtime – to distribute the vaccines essential to ending the pandemic.
Because of the unique challenges involved in producing and disseminating the vaccines – one required super-cold temperatures during transport, for example – manufacturers relied on the precision-made materials and pharmaceutical packaging expertise that USW members provide.
Members of Local 2-432, who work at Durba-Fibre in Menasha, Wis., made specialty laminated paperboard sleeves and inserts to protect the virus during shipment around the country. Members of Local 2175 in Bloomington, Minn., produced parts for Thermo King refrigeration units that helped trucks keep the vaccine cold on the road.
“I think a lot of people are just happy to help out in any way they can,” said Cole Wilhelm, a steward with Local 2175, noting the parts his members manufacture are typically used in motor coaches’ air-conditioning units and to keep items like produce cold during shipment.
The workers put in extra hours to meet vaccine manufacturers’ demand for their products, while realizing that the longer days boosted their chances of contracting COVID-19 on the job. Wilhelm said he and his colleagues know their work will help America turn the corner on the pandemic and noted, “It’s definitely a big motivator to get even more parts out the door.”
The urgent need for millions of doses of the vaccines generated skyrocketing demand not only for packaging materials and refrigeration units but precisely manufactured glass vials. At Corning, in Vinedale, N.J., and Nipro Glass, in Millville, N.J., USW members ramped up production at great personal sacrifice.
“The members are proud of what we do,” said Chris Ramirez, president of Local 701-01, whose members at the Corning plant make glass tubing that’s turned into vials. “We feel like we’re making a difference and helping other people.”
But even as workers put their safety at risk on the production floor, he said, company managers working remotely and in private offices had the audacity to resist the union’s call for common-sense COVID-19 safety measures.
“I try to tell them, you don’t feel what we feel. We’re out there. We’re in a war zone,” Ramirez said.
In nearly 27 years at Nipro Glass, Brian Banks, president of Local 219M, has never seen the company’s facilities so busy.
Banks’ plant makes tubing, which the adjoining Nipro facility converts into vials. Staffed at minimal levels for “quite a few” years, he said, the plants now rely on workers to put in 60- or 70-hour weeks both to fill a surge of orders and cover for co-workers sickened by COVID-19.
Some of his colleagues’ friends and relatives, including local health care workers, already received at least one dose of the vaccine. And while union members take satisfaction in helping to keep neighbors safe, he said, the unrelenting overtime takes its own toll on workers and their families.
Banks said the problem isn’t merely Nipro’s history of lean staffing but the decrepit state of American manufacturing overall. Just as the nation found itself unable to produce face masks and other personal protective equipment (PPE) when the pandemic struck, it now strains to produce the glass and other products necessary to rush the vaccines to the public.
“We used to have a lot more glass plants,” said Teresa Rodgers, Local 219M’s recording secretary, noting that the consolidation, closing and off-shoring of many facilities – including some once located in Millville – placed a “great demand on those of us that are still there.”
In Philadelphia, Local 286 and PCI Pharma Services – a pharmaceutical packaging company – closely collaborated to protect workers from COVID-19 and prepare for an eventual role in distributing vaccines.
The company provided enhanced PPE, installed Plexiglass dividers between work stations and cut each shift by a half-hour to keep groups of workers from having unnecessary contact with each other. Because of concern about workers contracting the virus on public buses and subway cars, the company provided reimbursements for shared-ride services and set up a private shuttle service that offered free rides to and from the plant.
Local 286 President Carlo Simone Jr. described the “unprecedented” safety measures as an outgrowth of the longstanding, strong working relationship between his local and the plant.
“It was a true partnership,” agreed Chris Blanton, vice president and general manager of PCI’s Philadelphia commercial operations, noting the company far exceeded federal infection-control guidelines “because keeping our workers safe is our No. 1 priority.”
“When you do the right thing – truly do the right thing – the financials will take care of themselves,” said Blanton, who praised union members for diligently performing their duties even when it wasn’t clear early in the pandemic just how easily the virus might be spread.
Because these measures helped to control the spread of the virus, PCI had hundreds of healthy workers ready to go when manufacturers approached the company for help packaging and distributing millions of doses of vaccines.
“It’s an exciting job, a very important job,” noted Penny Burroughs, a Local 286 steward and packer who’s worked at the plant for 35 years. “It’s something that’s going to be in the history books."