Safestart Objection Letter
To: Ben VanVeckhoven
March 23, 2017
Cc: Scott Cox
Subj: Objections to SafeStart
Ben,
As discussed yesterday during our conversation and as I offered, this letter is a formal and detailed explanation of our objections to SafeStart and it or any part of its program implementation into our site safety program(s).
To begin, we’ll address what we have identified as our principle objection which is the SafeStart Concepts. I’ve included a picture from SafeStart’s website in order to illustrate what SafeStart sells in their own words and that our objections are not hypothetical or mis-interpretations of what we “think” SafetStart is selling. The Representative stated in our meeting on March 14, 2017 that SafetStart is not “behavior based”, an “observation” program and it does not “blame the worker”. Interestingly, the material provided to us during the meeting which is identical to the picture below and the information on the SafeStart website clearly indicate the opposite. Everything about it is behavior based.
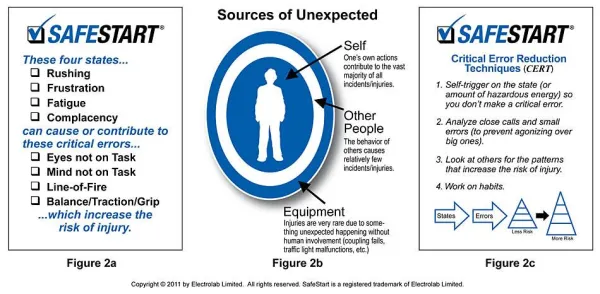
We wholeheartedly disagree with these concepts and cannot in good conscience endorse or promote these concepts to our membership or participate in such a program that promotes these concepts. We further cannot endorse or promote the Company utilizing its financial assets to purchase and sustain such a program that we believe is not the proper method in the prevention of injuries or illnesses. In the following statements, we’ll share with you what we believe and how it is in direct opposition to the SafeStart Concepts “state to error pattern” and “CERT’s”.
We do not believe that“one’s own actions contribute to the vast majority of all incidents/injuries.
We do not believe that“the behavior of others causes relatively few incidents/injuries.
We do not believe that“injuries are very rare due to something unexpected happening without human involvement (coupling fails, traffic light malfunctions, etc.)”.
We do believe that every workplace injury or illness is a result of exposure to a hazard and not the result of “one’s own actions” as SafeStart would have its customers believe.
We do believe that the actions or inactions of “others” contributes to more than “relatively few incidents/injuries” as SafeStart would have its customers believe.
We do believe that equipment fails and “something unexpected” does happen “without human involvement” more often than SafeStart would have its customers believe.
Also on this page (SafeStart Concepts), in discussing its “world-class or optimum safety system, SafeStart explains that; “more specifically, it focuses on the “human factors” (another way to say “behaviors”) that are involved in the majority of incidents and injuries”. Again, we do not believe that“one’s own actions contribute to the vast majority of all incidents/injuries. These concepts, as we can see from the SafeStart website are reiterated throughout the website and we have no reason to believe that these concepts will not be a focal point throughout SafeStarts training materials. These SafeStart Concepts should not be confused with what SafeStart refers to as “states” and “errors” and or the “state to error pattern”.
Another objection we have concerning SafeStart is that SafeStart does not discuss the hazards associated with workplace injuries or illnesses. We believe that in order to have what SafeStart refers to as a “critical error” on the part of the employee there must be a hazard present otherwise “one’s own actions” would not be considered erroneous or what SafeStart refers to as a “critical error” that increases the risk of injury. We believe that safety is a much greater science than the four (4) states, four (4) critical errors and application of CERT’s than SafeStart would have its customers believe. The Union’s preferred approach to safety and health focuses first and foremost on the hazards associated with the work, working conditions and working environment. The identification, evaluation, elimination, mitigation, substitution and control of hazards are not part of SafetStarts Concepts.
We believe, as does OSHA, ref: OSHA , that there must be proactive hazard identification and the subsequent use of a hierarchy of controls for each identified hazard. We view SafeStart as doing exactly the opposite in that it teaches and continues to train employees how to work around hazards or hazards that have been ignored or not identified. As we previously stated, we believe that in order to have what SafeStart refers to as a “critical error” on the part of the employee there must be a hazard present otherwise “one’s own actions” would not be considered erroneous or what SafeStart refers to as a “critical error” that increases the risk of injury. Employee exposure to hazards is always the cause of injuries or illness, not the way in which the employee failed to work around the identified or unidentified hazards.
Assume for a moment that SafeStart was implemented in the plant and there was an immediate decrease in workplace injuries and illnesses in the first year. Our concern is that with favorable results through SafeStart, the Company would not spend the necessary time, money or manpower to identify, evaluate, eliminate, mitigate, substitute or control hazards if it can simply teach and continue to train employees how to work around identified or unidentified hazards. Why would it? The fact of the matter is that the Company’s motivations for safety are driven by the same mechanism that all other aspects of the business are…bottom line profits. We strongly believe that without proactively identifying, evaluating, eliminating, mitigating, substituting and controlling hazards, when the SafeStart training fails, the hazards that were ignored or those hazards that failed to be identified and addressed due to focusing on SafeStarts concepts, “state to error patters” and “CERT’s” will still be present and the worker will still suffer an injury or illness.
Another objection we have to SafeStart comes from various sections of the SafeStart website. Statements made on their website such as; “focuses on unintentional errors and personal responsibility instead of rules, procedures and Company enforcement”, “raises awareness that our own actions account for the majority of our own injuries”, “incorporates a variety of adult learning principles to help solidify and retain the concepts”, “increasing “buy-in” to the concepts and overall program”, “it is efficient and cost effective and encourages personal responsibility for safety”, “and it paves the way for an observation and feedback process like SafeTrack”, “encourages personal responsibility and provides motivation for safety”.
We believe that it is the sole and legal responsibility of the Employer to provide a safe and healthy work environment for its employees, ref: Code of Alabama 1975 Section 25-1-1. We believe that the employees’ responsibility for safety is limited to his or her use of the work environment that the Employer provides within the confines of its intended application and design. Given the statements above from the SafeStart website, SafeStart, through an implied theory, would have our members believe that they are responsible for providing and maintaining a safe and healthy work environment AND using that environment while observing the “state to error pattern” and applying its CERT’s. This could not be more WRONG.
We also object to the implementation of the SafeStart “concepts”, “state to error pattern” and “CERT’s” into compliance training, RCA’s, JHA’s and SOP’s. More specifically, if inserted into an RCA, these concepts would always find the employee at fault for workplace injuries or illnesses and there could be no proof of such a claim. How could you prove that an employees’ “mind was not on task” or that his or her “eyes were not on task”? Sometimes, maybe more often than not, an employee is unaware that he or she could be in a particularly dangerous place or position or “line of fire” as referred to by SafeStart. These statements of error are so broad that they could easily be applied to almost any scenario even if they don’t truly apply. Further, JHA’s are for analyzing “hazards”, not to apply the SafeStart “state to error pattern” and “CERT’s”. Beyond that; our SOP’s do not adequately receive the revisions and updates that our members provide during our Job Cycle Checks. Some of these are critical operating instructions. By the time that an SOP is updated and provided to employees, whatever hazards are present and identified could have been long eliminated thus rendering the SafeStart “state to error pattern” and the application of “CERT’s” useless but, most importantly regarding the SOP’s, if one were to sit an think of all the potential hazards associated with a particular SOP, why wouldn’t the Company be more interested in evaluating, eliminating, mitigating, substituting or controlling those hazards instead? By this example alone, it should be clear that the SafeStart program as a whole, through its various reaches into the overall safety management system of our plant, would quickly set the Company’s focus in the wrong direction.
For all these reason, the Union cannot in good conscience endorse or promote these concepts to our membership or participate in such a program that promotes these concepts. We further cannot endorse or promote the Company utilizing its financial assets to purchase and sustain such a program that we believe is not the proper method in the prevention of injuries or illnesses.
The Union acknowledges and appreciates the efforts that the Company has made toward improving site safety in the last several years beginning with the survey conducted by PROSAFE, the report that was produced by PROSAFE and the efforts that the Company has made from that survey to establish a Steering Committee, Design Team, Internal Safety Audits, an upgrade in technology such as email, JD Edwards, Safety Suggestion Boxes and the agreement to allow for a Joint Environmental Health and Safety Committee recognizing a Union Chairperson just to name a few. The Union acknowledges that great strides have been made however, we also believe that there is more work to be done both by the Union and the Company. We believe that the ISA’s are a valuable tool in the identification of hazards and acknowledge that most of the hazards identified have been addressed and corrected however, some have not. We also believe that there are remaining hazards to be identified and that many hazards require technical expertise and knowledge that operators and maintenance technicians cannot provide. These will require a much greater effort on the part of engineering staff within the plant. Reliance on operators and maintenance personnel will generate a certain amount of information regarding hazards and they can be a great resource in the development and implementation of operating and safety systems since they have intimate working knowledge of their specific work environments, its systems and equipment and its capabilities and limitations however, they cannot provide all the Company needs in effectively identifying hazards or potential hazards.
With our current injury rate, we strongly believe that there is a better way to address the Company’s concerns than the purchase and sustainment of SafeStart, its concepts, the “state to error patter” and “CERT’s”. In fact, the Union offered the best program it is aware of during our recent contract negotiations to which the Company declined. The Triangle of Prevention (TOP) Program is a very manageable and sustainable program the Union could, would and does endorse and may likely be much cheaper than the cost of SafeStart. If you’d like to take a tour of a neighboring facility (SCA Barton) that has the TOP Program and see how truly valuable it can be, I’m sure that our Staff Rep. Scott Cox could assist in arranging a tour for you and other members of the management staff.
It is our sincerest hope that we can continue to work together toward a safer and healthier workplace and a more positive safety culture in our plant. Though we’ll have differences in opinion and practice, we think we share an overall common goal.
Sincerely and on behalf of USW Local 417-G,
Chris Parker
President